Packaging Circularity is Complicated
The topic of packaging sustainability and circularity is a complicated one. One consumer packaged goods (CPG) company may aim to reduce virgin plastic use, another may desire to make their packaging more recyclable, others focus on reducing the overall carbon footprint of their packaging, and so on. Another variable in the mix is regulation. Extended Producer Responsibility, or EPR, is a topic being discussed at the state level and has the potential to significantly impact how CPGs look at sustainability.
The reality is that packaging is vital to product protection and waste prevention, and the industry is continuously innovating to develop better packaging that meets the needs of its customers, the CPGs. Flexible packaging is a commonly used format because its lightweight characteristics significantly reduce material usage and cost throughout the value chain. Despite those advantages, the CPG industry stands at the forefront of a pressing environmental issue: How to develop circularity in flexible packaging.
To address the growing need for better packaging practices, numerous global CPGs aim to incorporate more recycled content into their packaging by 2030, intensifying the demand for recycled materials. Furthermore, CPGs must have these goals and make actual purchases, as it is not economically viable for recyclers to process materials without commercial use. Similarly, CPGs cannot incorporate recycled materials without a supply of them – a little bit of the "What comes first, the chicken or the egg?" argument. The clear message is that to make flexible packaging circular, many companies will need to take large strides.
Sustainable Packaging Requires Multiple Solutions
Various methods must be deployed for flexible packaging to meet its recyclability and sustainability goals. Despite the widespread use of flexible packaging, traditional collection and mechanical recycling has many challenges. The diversity of materials used in extrusion, such as polyethylene (PE), polypropylene (PP) and polyethylene terephthalate (PET), barrier materials, coatings and wet goods like adhesives and inks used for converting single-stream recycling. Meanwhile, inadequate infrastructure, consumer confusion and economic factors, such as the cost-effectiveness of using virgin materials and bulk density of flexible packaging in transit, present obstacles to scaling recycling efforts. Addressing these challenges is vital to meet the growing demand for recycled content in packaging.
Industry leaders are working together to provide two different types of recycling methods: Mechanical Recycling and Advanced Recycling. While mechanical processes efficiently handle common packaging formats, advanced techniques offer solutions for more complex and contaminated materials, such as Flexible Packaging, collectively contributing to a more comprehensive approach to recycling.
Mechanical Recycling: A Tradition of Sustainability
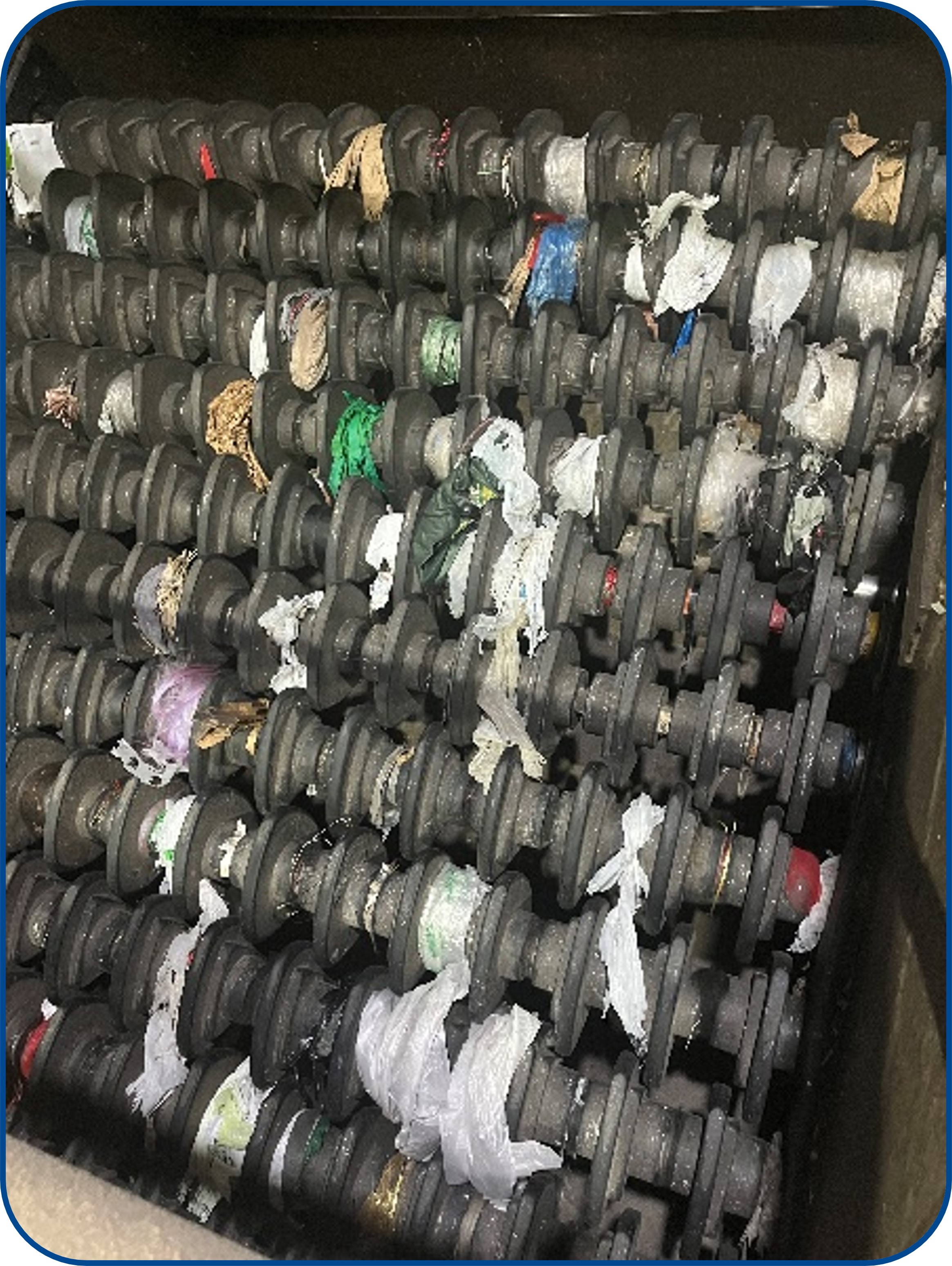
Mechanical recycling, often termed traditional recycling, refers to the mechanical action of sorting, size reduction and washing of waste so it can be reused. It encompasses a series of sequential steps to reclaim post-consumer or post-industrial materials.
In traditional streams, such as curbside recycling or collection at local municipalities, packaging waste is collected and transported to Material Recovery and Sortation Facilities (MRFs). Upon arrival, the recycling facility undertakes the crucial steps of sorting waste based on the material, shape, density and color to prevent contamination during the recycling process. Subsequently, the sorted materials undergo various processes to increase their bulk density and eliminate most dirt or residue. For plastics, the clean, shredded material is then melted and formed into pellets through extrusion and pelletization. These recycled plastic pellets serve as raw material for manufacturing various products, including containers, packaging, and other plastic items.
Mechanical recycling helps reduce the use of virgin plastics, easing the burden on natural resources and lowering greenhouse gas emissions. It requires less energy compared to producing new plastics, contributing to energy efficiency and reducing dependence on fossil fuels.
The process is not so simple for flexible packaging, so it is often excluded from traditional recycling outlets, like curbside and local collection at municipalities. Instead, mono-material flexible packaging, which is made primarily of HDPE, is recycled via the store-drop-off stream at many convenience stores in the United States. If these materials were collected in a traditional manner, they would pose a major problem for sortation equipment in traditional MRFs. Flexible packaging gets caught in the sortation machinery, leading to downtime and excessive wear. These store-drop-off materials are collected and recycled into HDPE pellets to be downcycled for applications like composite decking materials or back to flexible packaging.
Post-Consumer and Post-Industrial Recycled Materials
Before diving into advanced recycling methods, discussing the difference between post-consumer and post-industrial recycled materials is essential.
Post-industrial recycled, or PIR, materials have been commonplace in the industry for decades. The term PIR is somewhat nuanced, but in the case of film recycling, it refers to a more controlled and cleaner stream of very similar items that have not made it to an end consumer and mixed with other waste.
Post-consumer recycled materials refer to anything a consumer touches and then introduces to the recycling stream. These materials are incredibly variable and are often a mix of steel/aluminum cans, paper and corrugated materials, HDPE milk jugs and bottles, PET water and soft drink bottles, and much more. They also have residual products left in them and are dirty. This class of materials is what we traditionally think of when we consider recycled materials. It would also include any store-drop-off recycled materials, like HDPE grocery bags, plastic wraps and covers, as well as "back of the house" items, such as shrink wrap and secondary packaging.
Advanced Recycling: Innovation for the Future
Advanced recycling marks a transformative leap in waste management, particularly for the effective use of post-consumer and industrial plastics. This innovative approach employs cutting-edge techniques to convert mixed plastics into high-quality, recycled resin suitable for food- or industrial-grade use.
Advanced recycling is beneficial because it tackles many of the challenges posed by flexible packaging that traditional methods would struggle to process. In layperson's terms, advanced recycling can break down the many layers within post-consumer and post-industrial films to the molecular level, enabling the creation of virgin-like recycled plastic as those molecules are reformed to create new, recycled plastic resin. This depolymerization and polymerization process helps retain the quality of recycled materials and reduces the dependence on virgin resources, promoting a more sustainable and circular economy.
Another term frequently used in advanced recycling is "mass balance". Mass balance is a chain of custody technique used to track the movement and flow of recycled materials while estimating the amount of recycled content in refined goods. For example, if 20% by weight recycled material is introduced to the advanced recycling process, mass balance would estimate that 20% recycled material is exiting the process in the final product, minus process losses. This accounting is important, material exiting advanced recycling is virgin like, therefore its very difficult to empirically determine the amount of recycled material present. While mass balance provides a valuable tool for verifying claims about recycled content, it is an estimation. And since industrial processes are complex, the millions of pounds of material exiting recycling facilities will have variations in the final amount of recycled content.
Better Packaging. Better Life.
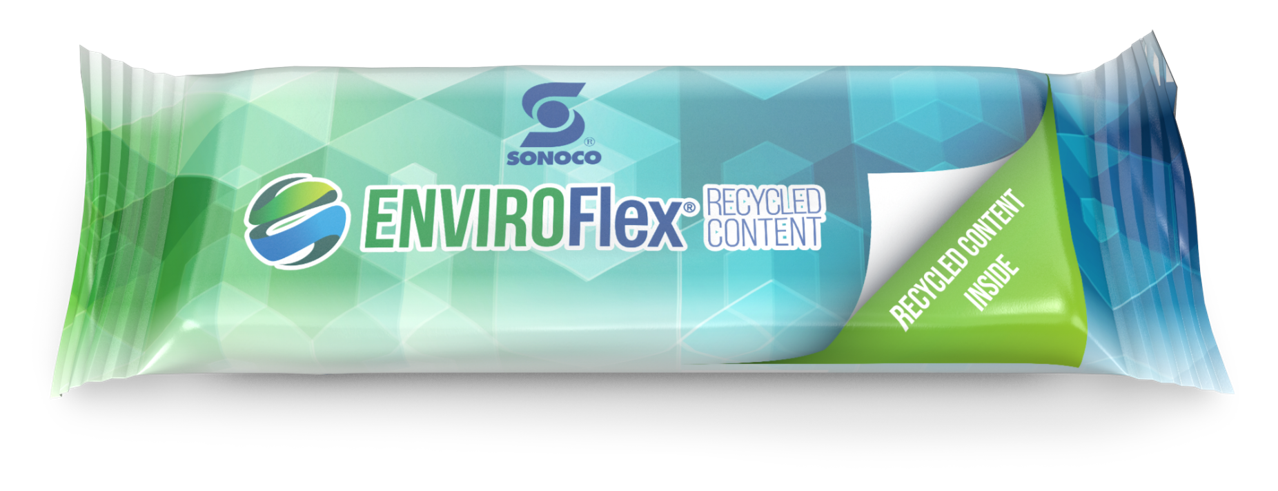
While flexible packaging offers unparalleled benefits, the demand for recycled content intensifies the need for effective recycling solutions. Embracing both mechanical and advanced recycling options is imperative for propelling CPG products toward a more circular economy and ensuring a sustainable future for flexible packaging, our planet and our lives.
Sonoco's EnviroFlex® Recycled Content: Flexible Structures Containing Post-Consumer and Post-Industrial Recycled Content
As a leader in sustainable packaging solutions, Sonoco offers its EnviroFlex Recycled Content rollstock laminations and pre-made pouches. Designed to meet the needs of various retail products, EnviroFlex Recycled Content is available in a range of barrier options and can incorporate zipper closures. EnviroFlex Recycled Content is suitable for a variety of products, including cookies and crackers, confections, coffee, dry/dehydrated foods, sweet and savory snacks, pet food and treats, personal care items and much more.
Reach out to the Sonoco Flexible Packaging team to learn more about our approach to sustainable flexible packaging
Eric Hair, Marketing Manager
Eric brings experience from application development and insights that supported innovation in the plastics industry. Today, as the marketing manager for our Flexible Packaging business, Eric oversees marketing strategy, as well as business and product development. He holds a degree in Chemical Engineering and an MBA from Clemson University.