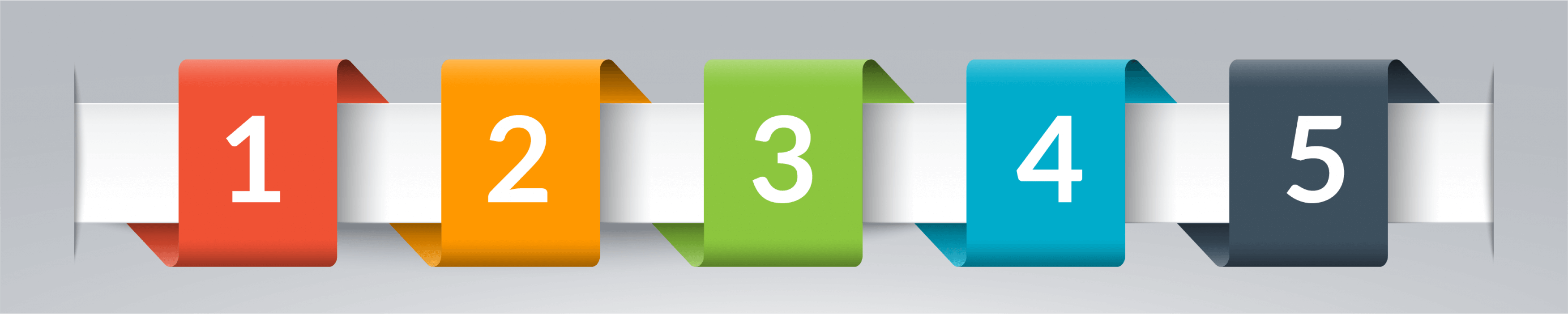
Turnkey Solutions Come from Decades of Packaging Experience
To the layman, medical device packaging seems straightforward and mundane. Put the device in a tray, put a lid on, seal it, and sterilize the packaging. But the fact is, every medical device package presents its own unique challenges for guaranteeing both sterility and safety.
That’s why medical device packaging specialists focus on precision, consistency and cleanliness in each design. To ensure success, it’s important to find industry-leading sealing machines and tooling coupled with medical device packaging material expertise. It’s easy if you follow these five “Steps.”
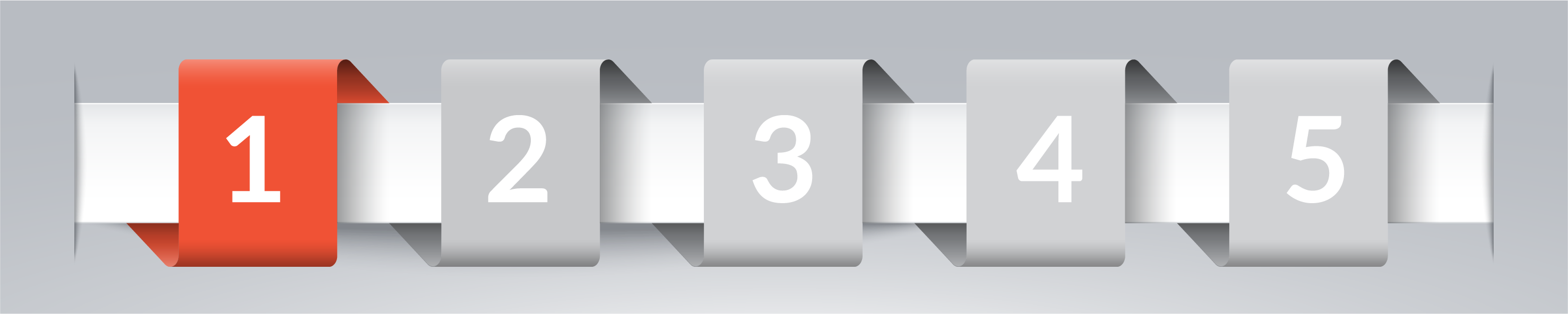
Step 1. Find Packaging Expertise
For every medical device packaging development project, the top priorities are product fit and consistent lid-to-tray integrity, both of which help maintain sterility and safety throughout the supply chain. Trying to reduce packaging costs or maximize line efficiencies unnecessarily is usually counterproductive and at the expense of reliable sealing.
Because the thoroughness of the packaging design process is paramount, the volume of packages usually does not have a big effect on price per package, material, or machine options selected. But thermoforming materials, equipment and sealing expertise always go together. Therefore, packaging engineers who understand how certain materials work best on different machines are often involved in designing the machines for optimal use with the desired materials. It is equally important that the package design is providing the necessary product protection when considering packaging materials and equipment. The Design Engineer is called upon to craft a package for form, fit and in-field function of the medical product.
The heat-seal tool that is installed into the sealing machine is inspected by the tooling manufacturer and/or the equipment manufacturer. The complete sealed package is then validated by an internal or external lab during official validation testing. This is when the heat-seal package receives its official stamp of approval as a certified medical package.
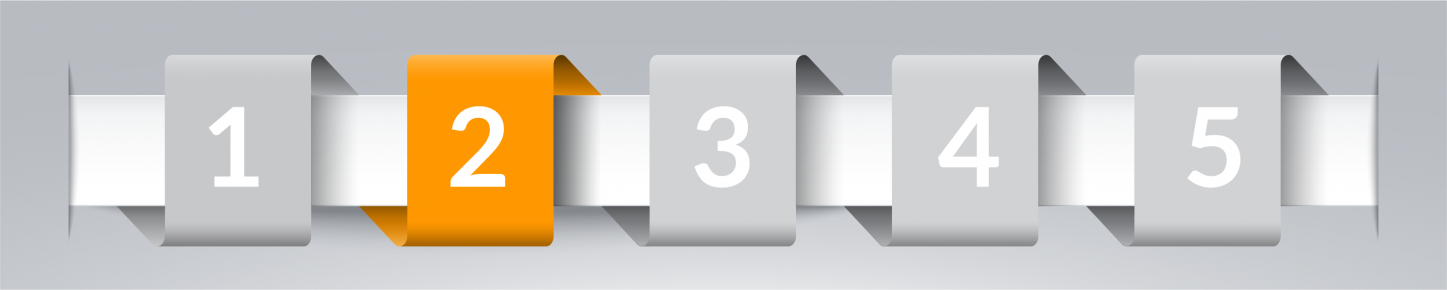
Step 2. Confirm Key Installation Parameters
Several factors aide in determining the proper machine required for the right medical sealing application. The available size of the clean room, product size and expected volumes all play an important role in deciding what sealing machine is best for the application. Additionally, machines with manual, semi-automatic and fully automatic loading feeders and power shuttles (where applicable) are available and can greatly speed up the packaging process for large runs.
There are many different levels of automation in heat-sealing equipment, but generally speaking, “rotary” turntable style machines have more automated features than “shuttle” left, right machines. Since the cycles per minute are often low in medical device packaging, the formula for choosing the right machine for the job must consider these factors.
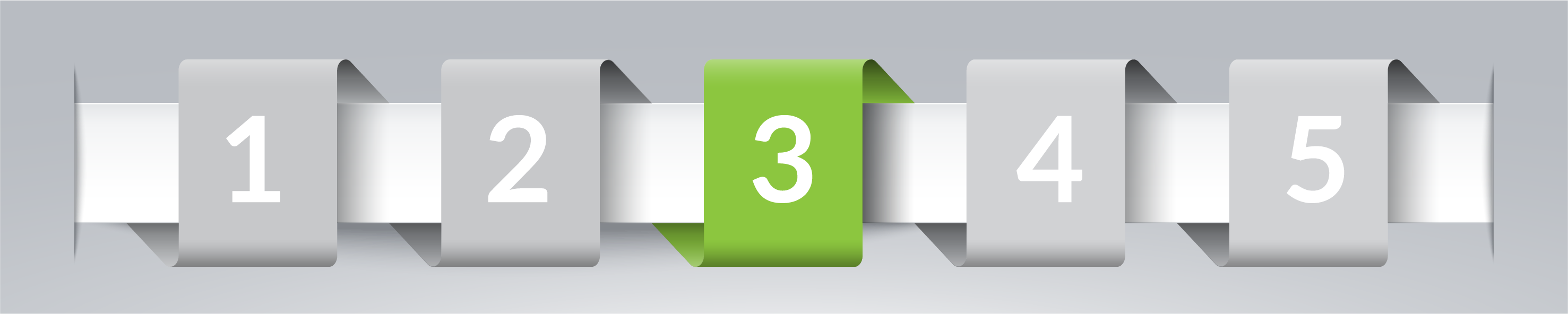
Step 3. Find a Proven Supplier
The medical industry tends to upgrade packaging equipment more frequently than other industries because they believe the latest and greatest technologies will produce the best, most reliable results. These companies also prefer policies like long warranties and on-call service professionals.
The tooling in modern heat-sealing applications is unique to customers and packages in that it conforms to the specific demands and measurements of each packaging project. For example, one machine can commonly accommodate more than 100 sets of tooling. Always learning from their customers, seasoned, proven suppliers can respond quickly to packaging modifications because they avoid common pitfalls in engineering and design.
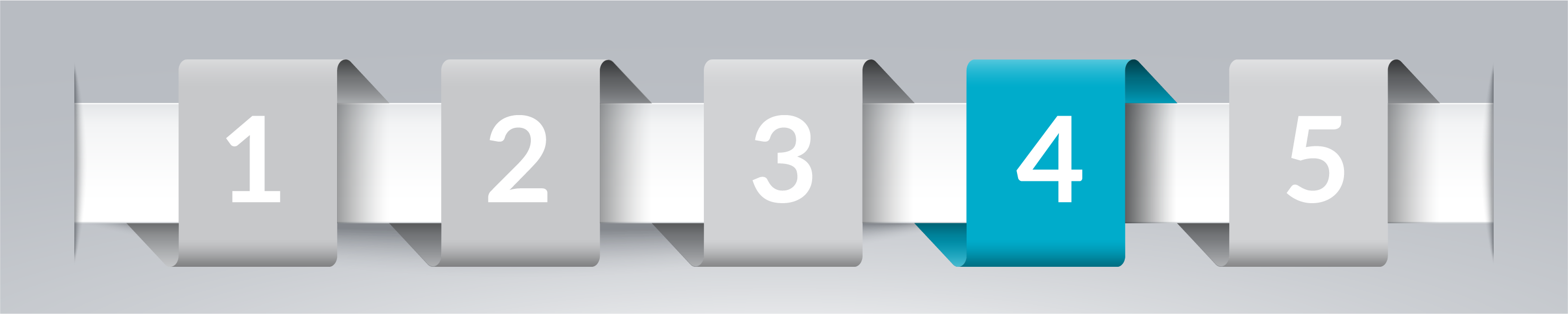
Step 4. Choose Reliable Heat-Sealing Equipment
Consistency in heat and pressure are the most critical performance criteria for reliable heat-sealing equipment. That means the machine must apply the precise amount of temperature, time/dwell and pressure consistently across all seal areas.
Recent innovations have increased both the heat consistency and ease of machine maintenance. Machines with a single-element casted platen are delivering the most consistent heat transfers, and designs for drawer-style loading of heat plates can now be replaced by one operator.
Medical devices are demanding more complex designs that can protect and secure the product—and packaging—from damage. Heat sealing equipment should be able to easily accommodate unusual shapes, such as “island” seals in the middle of packaging, and deep depth products. That’s why it’s always advisable to have production tooling designed and manufactured in-house by the equipment supplier to avoid costly mistakes or communication errors.
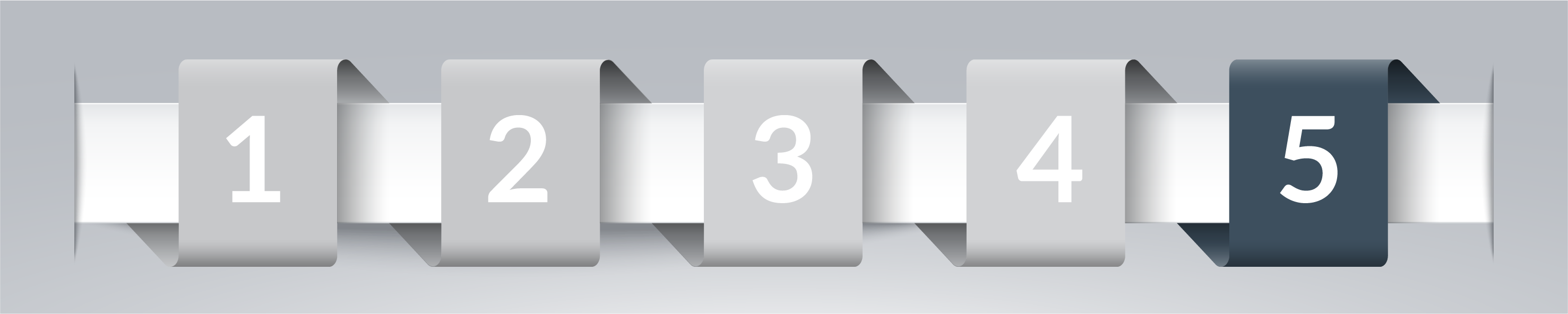
Step 5. Perform Due Diligence Before Validation Testing
Many medical device packaging processes must be validated for safety and sterility by the customer or a third-party compliance lab. Not just the sealing equipment, but the different packages running on it as well. For validation to occur, the packages must be filled with the actual medical devices for validation testing – so be prepared to supply 29 devices for 90/90 reliability validation or 59 devices for 95/95 reliability validation.
Medical device packages fail the first attempt at compliance validation testing. To avoid testing delays, your best bet is to find suppliers who offer integrated design services and know the medical packaging industry. With a little bit of knowledge and some preparation, you will be launching your medical package to market much sooner than your competition.
Blog By: Rob Arneson, Sonoco Alloyd Sales Manager, Machinery; and Sarah Rosenblum, Packaging Compliance Labs Sr. Director of Sales & Marketing
Contact the Sonoco Alloyd Team today to learn more about our medical device packaging options.